The Challenges and Opportunities
of Flexible Parts Feeding in the Automotive Sector
Introduction: The Global Automotive Sector
The automotive sector, valued at around $3.5 trillion in 2021 with a projected increase to over $4.5 trillion by 2025, plays a pivotal role in driving technological innovation, environmental sustainability, and economic growth worldwide.
The Evolving Landscape: Technological Innovations and Production Challenges
The industry, one of the most industrialized sectors, confronts continual challenges. These arise from fluctuating consumer demands, stringent regulations, and technological advancements necessitating resourceful and sustainable management.
Embracing Industry 4.0: The Shift Towards Flexible Parts Feeding
With the rise of Industry 4.0 technologies, automotive manufacturers are under increasing pressure to adapt their production lines. Central to this transformation is flexible parts feeding, an approach allowing for greater adaptability in handling a wide array of automotive components.
Cylindrical
Complex
Flat
Automotive parts feeder: The Case of FlexiBowl®
FlexiBowl® is a leading example of Automotive parts feeder, offering multiple advantages such as:
- Versatility: FlexiBowl® can handle a variety of part shapes, sizes, and materials, eliminating the need for multiple feeders.
- Increased Efficiency: The technology reduces downtime due to feeder changeovers, increasing production speed.
- Adaptability: It allows rapid and smooth transitions between different parts, improving overall workflow.
A flexible feeder like FlexiBowl® can be implemented in various production processes, particularly when dealing with components ranging in size from 1 to 300 mm.
- Assembly: In the assembly of automotive components or subsystems, a Flexibowl can be used to supply parts of varying sizes to the assembly line, adapting its operation based on the size of the component being handled.
- Metalworking: During metalworking, such as milling, turning or grinding, a flexible feeder can supply differently sized parts to the machine tool for various types of machining.
- Moulding processes: In the manufacturing of plastic or metal parts, a flexible feeder can be used to handle the molded components, but not the materials required for the molding process, such as plastic granules or metal powder.
- Painting and finishing: A flexible feeder can be used in the painting and finishing process, handling the components and semi-finished products that need to be painted.
- Inspection and quality control: During component inspection and quality control, a flexible feeder can be used to supply robots with the components that need to be presented to inspection devices, such as machine vision systems or sensors.
Flexible Parts Feeding: The Advantages of FlexiBowl®
FlexiBowl® is a pioneering solution in flexible parts feeding technology. It stands out for its multitude of benefits, including:
-
- Ease of Integration
FlexiBowl® is designed to seamlessly fit into any production project, making its incorporation into existing systems straightforward and efficient. - Production Flexibility
The system allows for easy adaptation to any production changes, reflecting its innate flexibility and adaptability. - Robot and Cobot Compatibility
FlexiBowl® can be integrated with all robots and cobots on the market, making it a versatile choice for a wide array of manufacturing processes. - Accurate Parts Recognition and Orientation
FlexiBowl® ensures precise recognition and positioning of various components, boosting overall productivity and minimizing errors.
- Ease of Integration
Types of Components an Automotive parts feeder Can Handle
- Screws and bolts: These are common components in the automotive industry that a flexible feeder can handle, especially in automated assembly operations.
- Bushings and bearings: These medium-sized components are also common in the automotive industry and can be handled by a flexible feeder.
- Electrical components: Items such as connectors, switches, relays, fuses and other electronic components can be handled by a flexible feeder.
- Engine parts: Some smaller engine parts, such as pistons, connecting rods, valves, can be handled by a flexible feeder.
- Plastic components: Various plastic parts, such as interior components, fasteners, housings, small covers, light components, and other bodywork pieces up to a maximum size of 300 mm, can be handled by a flexible feeder like FlexiBowl®.
Embracing the Future of Automotive Production
The future success of the automotive industry depends on its ability to adapt, innovate, and respond to an evolving production landscape. Herein, flexible parts feeding devices like FlexiBowl® are set to play a pivotal role.
Videos
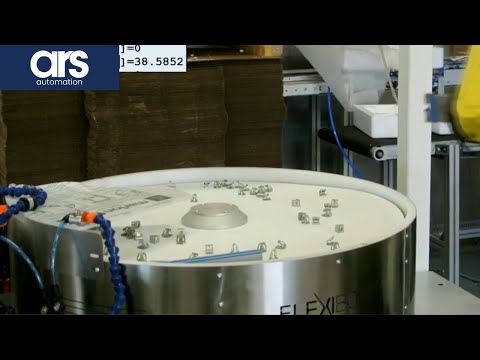
18 x 20 mm

50 x 25 mm

28 x 13 mm

20 x 5 mm
What are the benefits of using a FlexiBowl® system in automotive assembly processes?
FlexiBowl® is a flexible feeding device that can be smoothly integrated with every robot and vision system brand. Entire families of parts within 1-250 mm and 1-250 g can be handled by a single FlexiBowl® replacing a whole set of dedicated vibratory bowl feeders. No more parts jams and exhausting mechanical adjustments.
Its lack of dedicated tooling and its easy to use and intuitive programming software allows quick and multiple product changeovers inside the same work shift.
A lean and reliable design guarantees predictable and low maintenance costs and makes it the suitable feeding solution for the Automotive industry.
Main end users

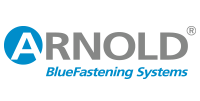
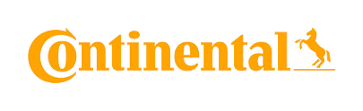
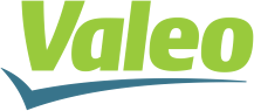
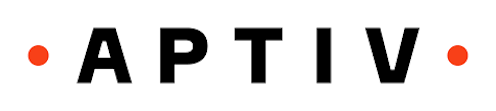
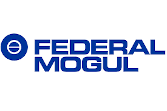
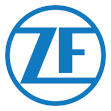
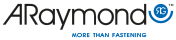
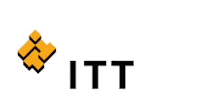

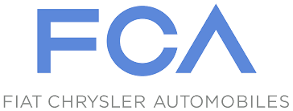
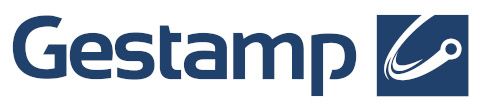
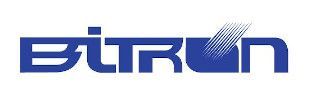
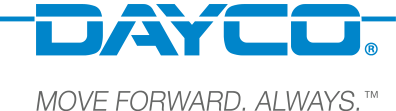
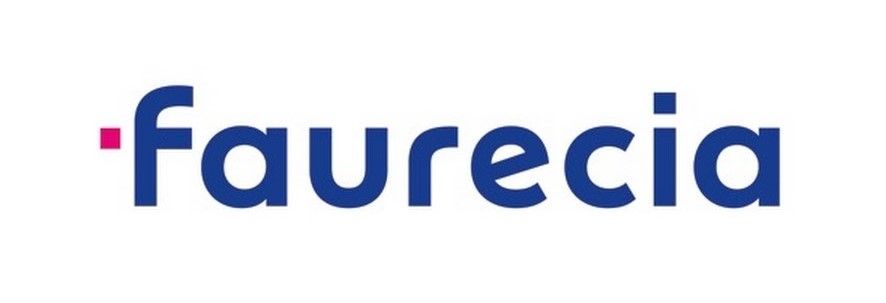
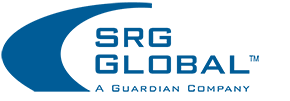
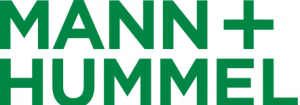

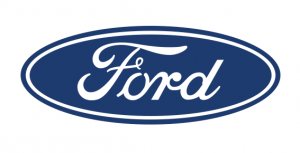