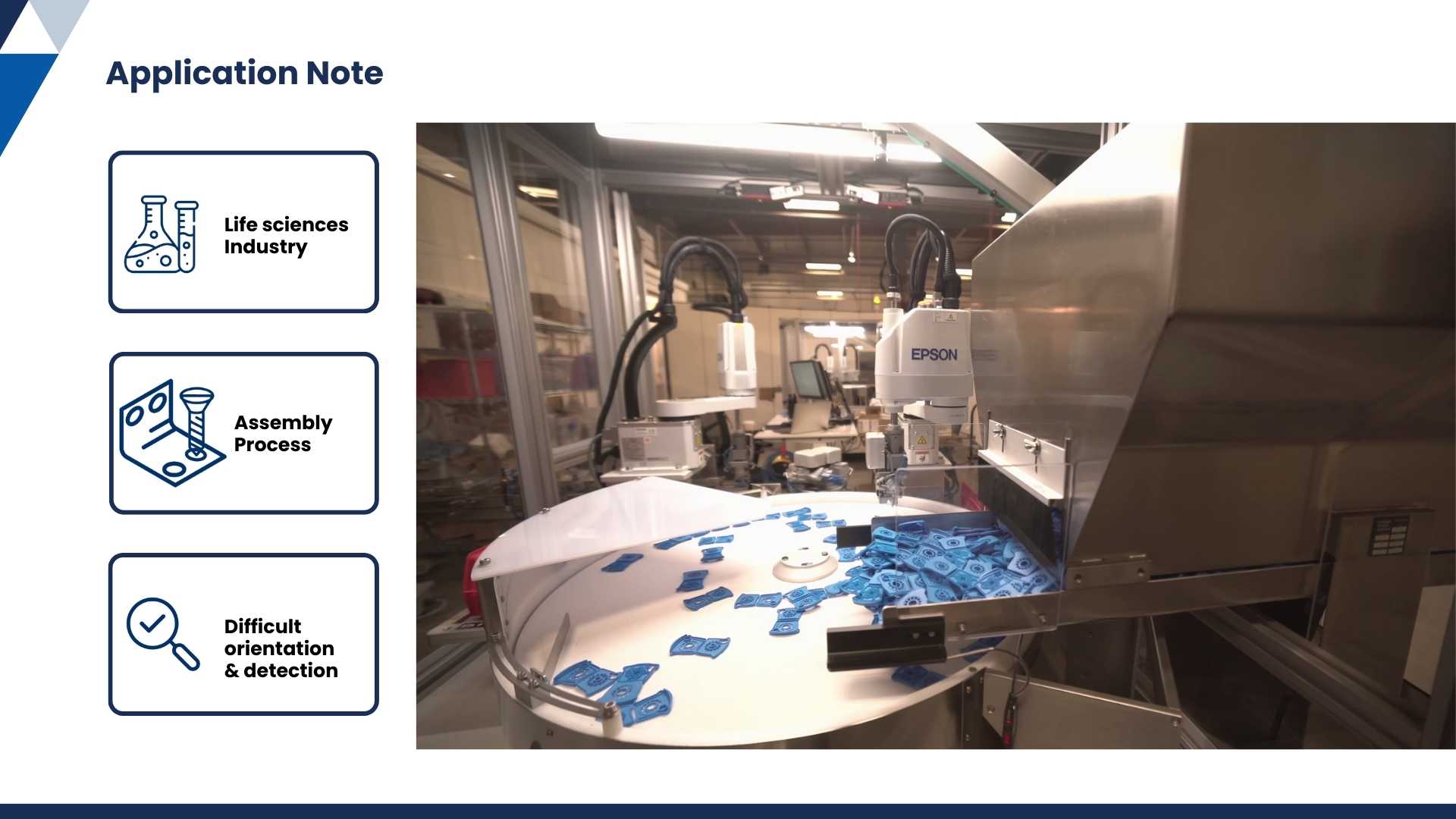
Flexible Feeding in Medical Manufacturing: Streamlining COVID-19 Test Assembly
Case study: the integration of a flexible system designed to handle complex components with precision, boosting efficiency with a high throughput of 35 parts per minute
Our partner
Dynamic Automation & Robotics is a custom automation integrator that is focused on customer satisfaction, service and support. The company all-inclusive project management style allows its customers to play a major role in engineering decisions throughout the life cycle of the project. Every machine comes with a custom operations manual including a preventative maintenance schedule. They offer short and long term service agreements and have decades of experience servicing their clients needs worldwide.
The Challenge
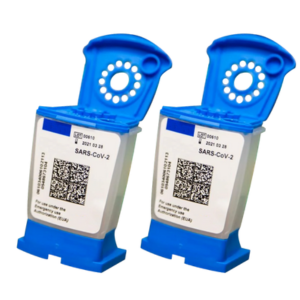
- Implement an optimized flexible automation system for the assembly of COVID-19 diagnostic tests .
- Feed three different products on a single line, optimizing the production layout.
- Handle non-rigid materials and parts that are difficult to orient and detect.
- Provide a smooth part changeover transition.
The Solution
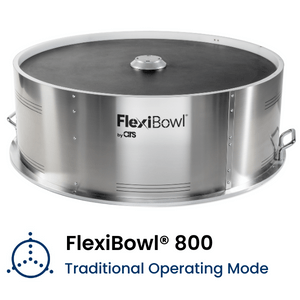
- Integration of a flexible feeding system FlexiBowl® 800 , equipped with quick emptying for rapid production changeover.
- Use of the Epson vision system for precise part identification.
- Deployment of two Epson robots for picking and loading parts onto an external swivel unit.
- Inclusion of a high-speed airveyor system for efficient part transfer.
The Benefit
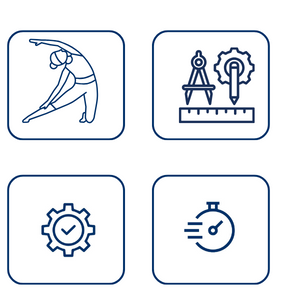
- Greater flexibility and adaptability in the production system.
- Achievement of a compact and optimized layout.
- Improvement in production quality by automatically feeding non-rigid products that are difficult to orient and detect.
- Enhancement of the production process, with a feed rate of 35 parts per minute.
The case study focuses on Dynamic Automation's innovative approach to addressing the challenges presented by the COVID-19 pandemic in the medical and pharmaceutical industry. Faced with the need for precise handling of complex products, Dynamic Automation implemented a flexible automatic system. This system was designed to enhance the assembly process for COVID-19 diagnostic tests, managing three distinct products within one efficient system.
A critical aspect of the project was the integration of a FlexiBowl® 800 system, which separates and pre-orients parts. Subsequently, an Epson vision system identifies each part, and two Epson robots are employed for precise picking and loading. The FlexiBowl® system allows for handling multiple product types on a single line while maintaining a compact and efficient layout, crucial for rapid changeovers and meeting dynamic market demands.