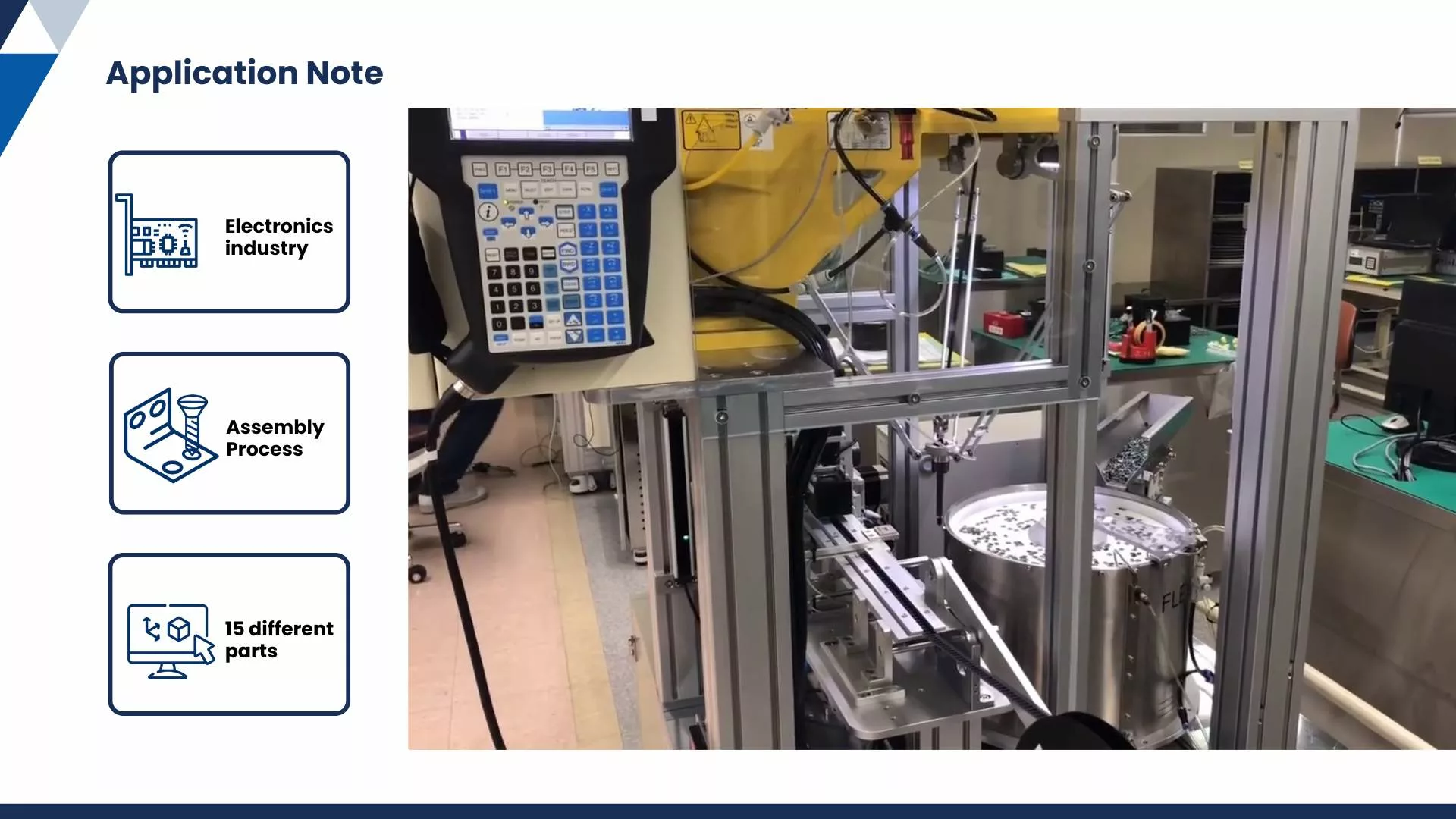
The system enables the efficient feeding and processing of 12 models of microchips within a compact and scalable layout.
Case Study: The assembly cell consists of a series of stations dedicated to the assembly of microchips.
Our partner
AIM Company specializes in providing innovative and flexible automation solutions for industrial applications. Their mission is to simplify the adoption of robotic technologies by automating repetitive tasks, allowing businesses to improve efficiency and focus on higher-value operations.
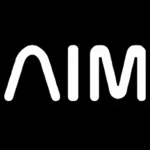
The Challenge
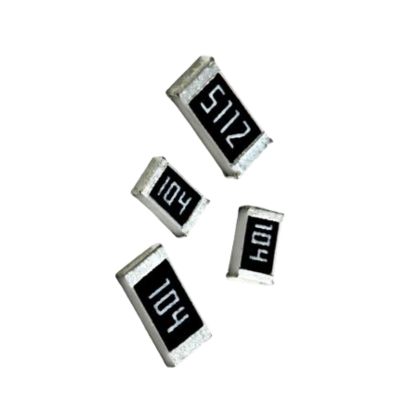
- Feeding delicate microchips of 4 x 6 mm (0.15 x 0.23 in) with precision, ensuring compliance with ESD requirements to protect sensitive components.
- Ensuring consistent delivery of over 40 parts per minute, with a maximum output of 50 ppm, while maintaining a tolerance of 0.1 mm for precise alignment and positioning.
- Handling 12 different microchip models without the need for extensive reconfigurations, in a compact layout optimized for seamless integration into production lines.
The Solution
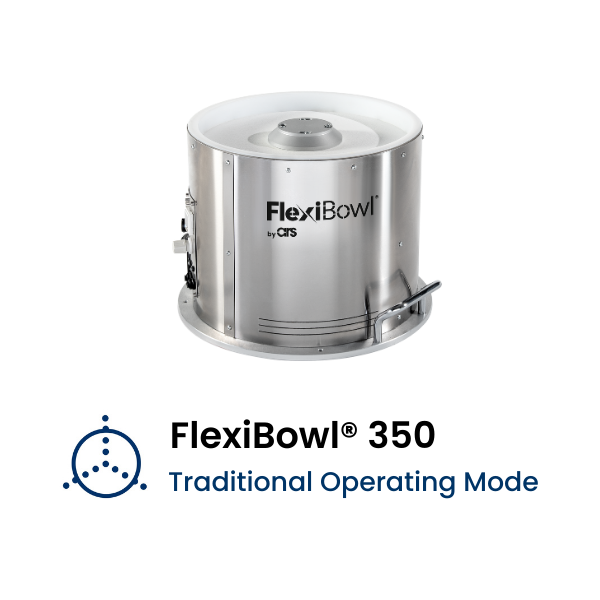
- The FlexiBowl® 350, equipped with an anti-static disc, ensures safe and precise handling of delicate and small components.
- The 5 MP vision camera guarantees exceptional precision, maintaining a tolerance of 0.1 mm.
- The 90° tilt unit enables smooth and efficient part handling, achieving a throughput of up to 30 ppm.
- The FANUC robot with a universal EOAT system provides reliable and versatile pick-and-place operations for various component types.
- The compact and modular layout supports quick changeovers and allows for future scalability.