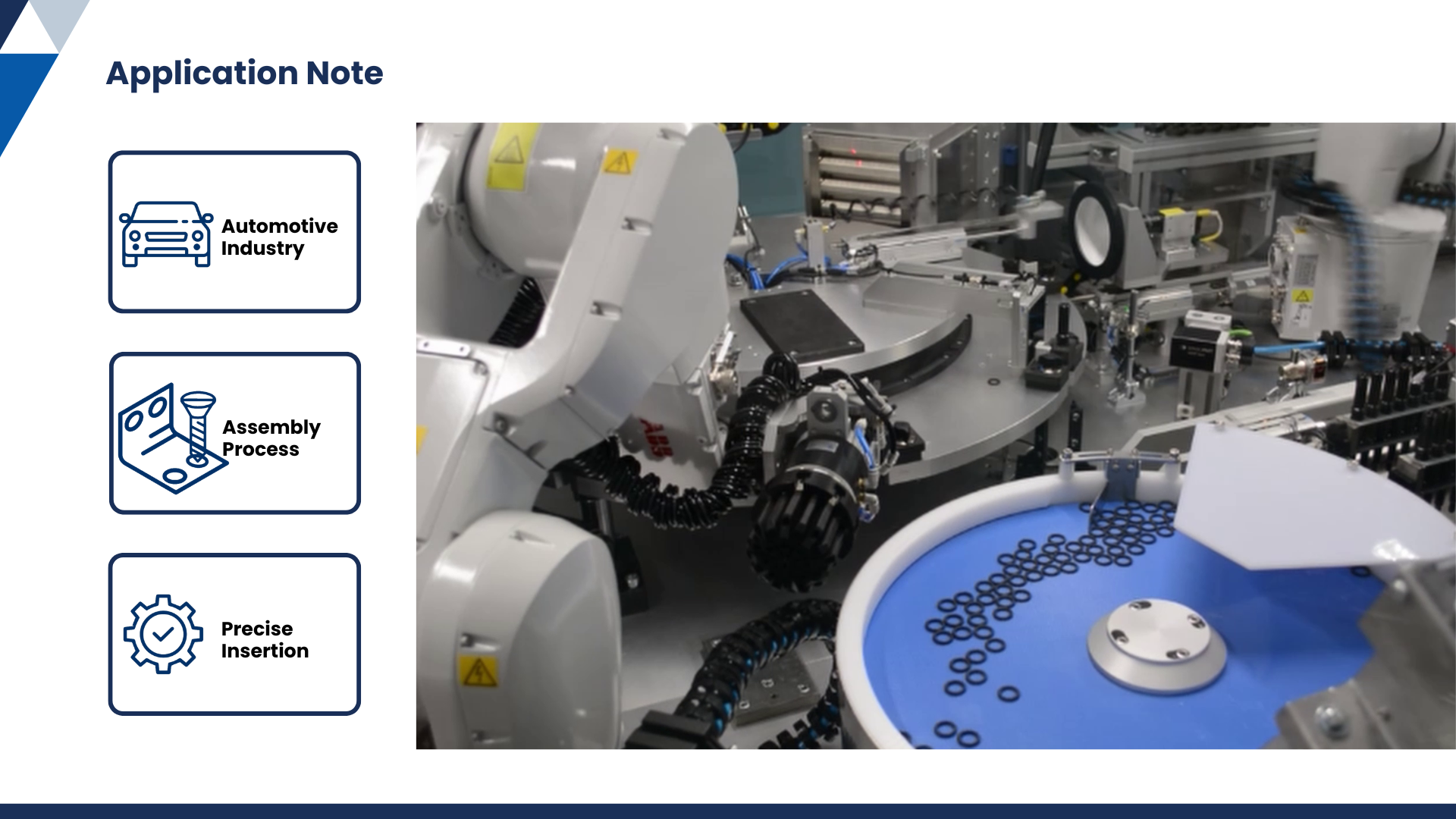
The system ensures efficient assembly of six connector models within a flexible and scalable layout.
Case study: the assembly cell consists of a set of stations dedicated to the assembly and testing of injection connectors for the automotive sector.
Our partner
From 1975, Samac provides customized equipment for automated assembly and testing processes of mechanical, electromechanical and hydromechanical components. The service starts from the development of the solution to the after-sales, passing through the design, manufacturing and installation.
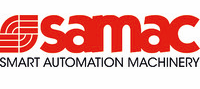
The Challenge
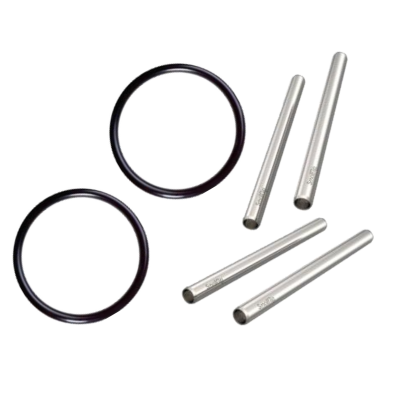
- Manage several different parts with varying shapes and dimensions.
- Handle sticky and non-rigid materials efficiently.
- Ensure ultra-precise insertion to meet quality standards.
- Adapt to a tight layout while maintaining high productivity.
The Solution
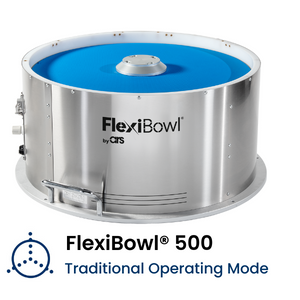
- 2 FlexiBowl® 500: flexible feeders for precise component handling.
- ABB 6-axis robot for automated pick-and-place operations.
- Custom-designed double EOAT for simultaneous handling of multiple components.
- Compact and modular layout, designed to support future expansions.
The Benefit
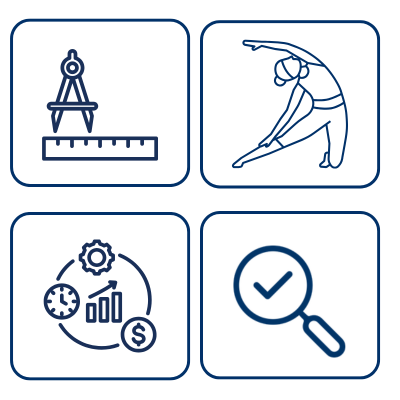
- Compact design: optimizes productivity within tight production layouts.
- Flexible handling: efficiently manages multiple part types with varying geometries.
- Optimized cycle time: achieves a production time of 12 seconds per part, ensuring high throughput.
- Precision assembly: ensures ultra-accurate insertion to meet strict quality standards, handling sticky and non-rigid components seamlessly.